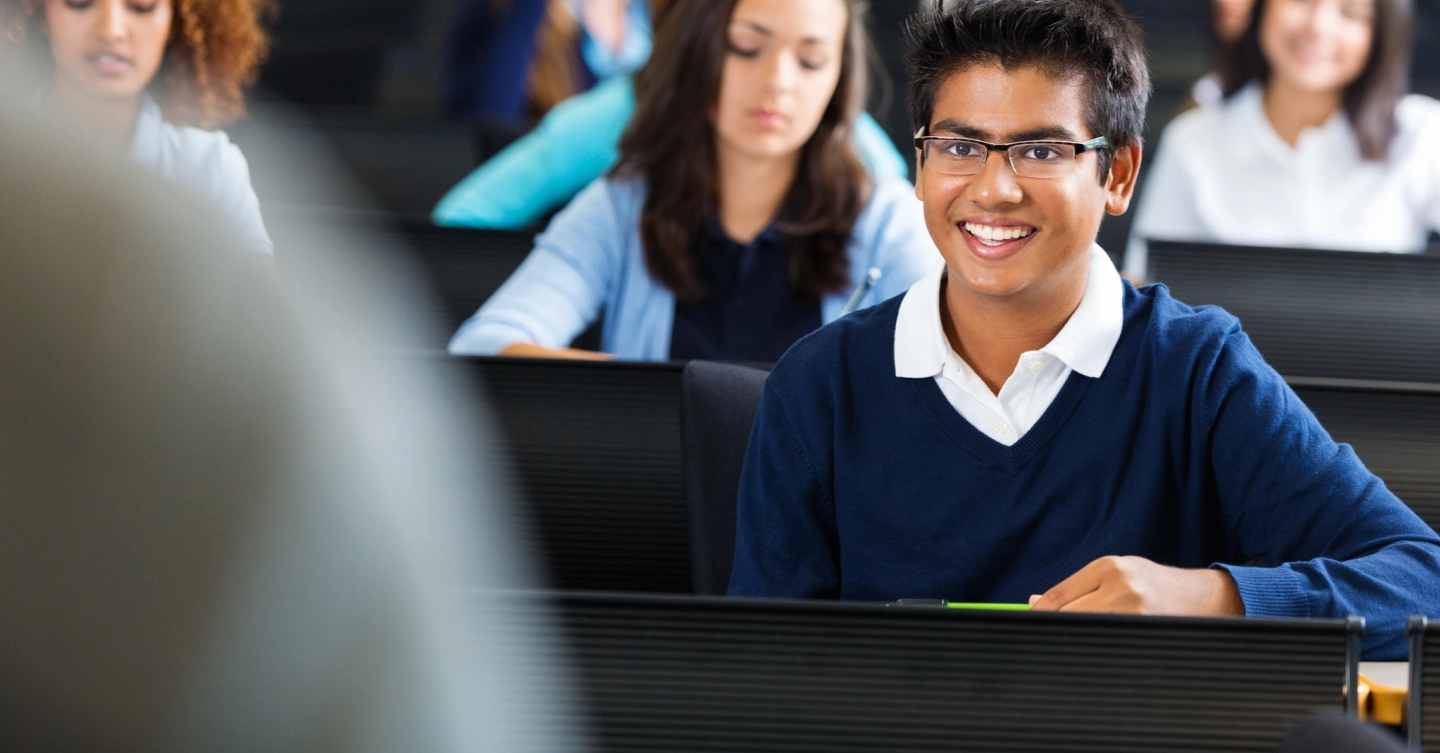
Simplify Learning with Milestone Your Trusted Education Partner
At Milestone, We are committed to providing a complete education solution in Thane. Our mission, values, and key principles shape our behavior to allow us to continually provide a high-quality, hassle-free education experience for our Accredited Partner Centres and students.
Know moreDiscover Lifelong Learning with Curated Masterclasses
-
AI Integrated CurriculumView Course
Masters In Data Analysis and Data Science with AI
4.5 / 5
1500+ Reviews
Placement Assistance
Practical Training
Expert Faculty
MIT Certification
32 Weeks
Advance
50+ Active Learners
-
Engineering the Future with PrecisionView Course
Masters In Product Design & Analysis
4.5 / 5
1500+ Reviews
100% Job Guarantee
Practical Training
Expert Faculty
Govt. Certification
32 Weeks
Advance
120+ Active Learners
-
Designing Tomorrow's Infrastructure TodayView Course
Masters in Civil Design
4.5 / 5
1500+ Reviews
100% Job Guarantee
Practical Training
Expert Faculty
Govt. & Autodesk Certification
32 Weeks
Advance
130+ Active Learners
-
Innovative Designs for Modern LivingView Course
Masters in Interior Design
4.5 / 5
1500+ Reviews
100% Job Guarantee
Practical Training
Expert Faculty
MIT Certification
32 Weeks
Advance
100+ Active Learners
-
Driving Industrial Progress through AutomationView Course
Masters in Industrial Automation
4.5 / 5
1500+ Reviews
100% Job Gaurantee
Practical Training
Expert Faculty
MIT Certification
24 Weeks
Advance
100+ Active Learners
-
Crafting Architectural MasterpiecesView Course
Masters in Architectural BIM
4.5 / 5
1500+ Reviews
100% Job Gaurantee
Practical Training
Expert Faculty
Govt. & Autodesk Certification
36 Weeks
Advance
110+ Active Learners
-
Your First step in AIView Course
Python Programming
4.5 / 5
1500+ Reviews
Placement Asistance
Practical Training
Expert Faculty
MIT Certification
6 Weeks
Foundation
75+ Active Learners
-
Innovate with Data, Lead with KnowledgeView Course
Python Programming With Data Science
4.5 / 5
1500+ Reviews
Placement Assistance
Practical Training
Expert Faculty
MIT Certification
8 Weeks
Advance
100+ Active Learners
-
Transforming Data into DecisionsView Course
PG in data Analytics
4.5 / 5
1500+ Reviews
Placement Asistance
Practical Training
Expert Faculty
MIT Certification
24 Weeks
Advance
90+ Active Learners
-
Empowering the Future with DataView Course
PG in Data Science with AI & ML
4.5 / 5
1500+ Reviews
Placement Asistance
Practical Training
Expert Faculty
MIT Certification
24 Weeks
Advance
80+ Active Learners
-
Transition to Technical WorldView Course
Mechanical Draughtsman
4.5 / 5
1500+ Reviews
Placement Assistance
Practical Training
Expert Faculty
MIT Certification
12 Weeks
Foundation
10+ Active Learners
-
Engineering Precision, Designing ExcellenceView Course
AutoCAD Mechanical
4.5 / 5
1500+ Reviews
Placement Asistance
Practical Training
Expert Faculty
Govt. & Autodesk Certification
8 Weeks
Foundation
550+ Active Learners
-
Designing Tomorrow's Machines TodayView Course
Solidworks
4.5 / 5
1500+ Reviews
Placement Asistance
Practical Training
Expert Faculty
Govt. & Autodesk Certification
8 Weeks
Foundation
300+ Active Learners
-
Innovative Engineering for Modern ChallengesView Course
NX
4.5 / 5
1500+ Reviews
Placement Asistance
Practical Training
Expert Faculty
Govt. Certification
8 Weeks
Foundation
230+ Active Learners
-
Engineering the Future with PrecisionView Course
Catia
4.5 / 5
1500+ Reviews
Placement Assistance
Practical Training
Expert Faculty
Govt. Certification
8 Weeks
Foundation
175+ Active Learners
-
Innovate, Design, CreateView Course
Creo
4.5 / 5
1500+ Reviews
Placement Assistance
Practical Training
Expert Faculty
Govt. Certification
8 Weeks
Foundation
150+ Active Learners
-
Building the Future with Mechanical MasteryView Course
Inventor
4.5 / 5
1500+ Reviews
Placement Assistance
Practical Training
Expert Faculty
Govt. Certification
8 Weeks
Foundation
125+ Active Learners
-
Mechanical Minds, Creative DesignsView Course
Fusion360
4.5 / 5
1500+ Reviews
Placement Assistance
Practical Training
Expert Faculty
Govt. Certification
8 Weeks
Foundation
100+ Active Learners
-
Precision Engineering for Tomorrow's ChallengesView Course
Revit MEP BIM
4.5 / 5
1500+ Reviews
Placement Assistance
Practical Training
Expert Faculty
Govt. Certification
8 Weeks
Foundation
425+ Active Learners
-
Building Strong Foundations for the FutureView Course
Ansys
4.5 / 5
1500+ Reviews
Placement Assistance
Practical Training
Expert Faculty
MIT Certification
8 Weeks
Intermediate
65+ Active Learners
-
Crafting Solutions with Mechanical IngenuityView Course
GD&T
4.5 / 5
1500+ Reviews
Placement Assistance
Practical Training
Expert Faculty
MIT Certification
2 Weeks
Foundation
200+ Active Learners
-
Transition to Technical WorldView Course
Architectural Draughtsman
4.5 / 5
1500+ Reviews
Placement Assistance
Practical Training
Expert Faculty
MIT Certification
12 Weeks
Foundation
300+ Active Learners
-
Precision in Every PlanView Course
AutoCAD Architecture
4.5 / 5
1500+ Reviews
Placement Asistance
Practical Training
Expert Faculty
Govt. Certification
8 Weeks
Foundation
220+ Active Learners
-
Design Your Dream InteriorsView Course
Sketchup
4.5 / 5
1500+ Reviews
Placement Asistance
Practical Training
Expert Faculty
MIT Certification
2 Weeks
Foundation
175+ Active Learners
-
Building the World, One Design at a TimeView Course
Revit Architecture
4.5 / 5
1500+ Reviews
Placement Asistance
Practical Training
Expert Faculty
Govt. & Autodesk Certification
8 Weeks
Foundation
150+ Active Learners
-
Crafting Beauty in Every CornerView Course
3Ds Max
4.5 / 5
1500+ Reviews
Placement Assistance
Practical Training
Expert Faculty
Autodesk Certification
8 Weeks
Foundation
125+ Active Learners
-
Render Your Dreams with perfectionView Course
Vray
4.5 / 5
1500+ Reviews
Placement Assistance
Practical Training
Expert Faculty
MIT Certification
2 Weeks
Foundation
100+ Active Learners
-
Where Creativity Meets FunctionalityView Course
Lighting Design
4.5 / 5
1500+ Reviews
Placement Assistance
Practical Training
Expert Faculty
MIT Certification
6 Weeks
Advance
90+ Active Learners
-
Designing Efficiency, Engineering SuccessView Course
Navisworks
4.5 / 5
1500+ Reviews
Placement Assistance
Practical Training
Expert Faculty
Autodesk Certification
8 Weeks
Intermediate
50+ Active Learners
-
Transforming Spaces, Inspiring LivesView Course
Civil Draughtsman
4.5 / 5
1500+ Reviews
Placement Assistance
Practical Training
Expert Faculty
MIT Certification
12 Weeks
Foundation
300+ Active Learners
-
Precision in Every PlanView Course
AutoCAD Civil
4.5 / 5
1500+ Reviews
Placement Asistance
Practical Training
Expert Faculty
Govt. & Autodesk Certification
8 Weeks
Foundation
210+ Active Learners
-
Designing the FoundationsView Course
Revit Structure
4.5 / 5
1500+ Reviews
Placement Asistance
Practical Training
Expert Faculty
Autodesk Certification
8 Weeks
Foundation
175+ Active Learners
-
Innovative Designs for Robust InfrastructureView Course
Tekla
4.5 / 5
1500+ Reviews
Placement Asistance
Practical Training
Expert Faculty
MIT Certification
8 Weeks
Foundation
150+ Active Learners
-
Engineering Stability, Designing StrengthView Course
Staad Pro
4.5 / 5
1500+ Reviews
Placement Asistance
Practical Training
Expert Faculty
MIT Certification
8 Weeks
Foundation
135+ Active Learners
-
Shaping the World with Structural ExcellenceView Course
Etab
4.5 / 5
1500+ Reviews
Placement Asistance
Practical Training
Expert Faculty
MIT Certification
8 Weeks
Foundation
100+ Active Learners
-
Precision in Every PlanView Course
Interior Draughtsman
4.5 / 5
1500+ Reviews
Placement Assistance
Practical Training
Expert Faculty
MIT Certification
12 Weeks
Foundation
300+ Active Learners
-
Bringing Interiors to LifeView Course
AutoCAD Interior
4.5 / 5
1500+ Reviews
Placement Assistance
Practical Training
Expert Faculty
Govt. & Autodesk Certification
8 Weeks
Foundation
230+ Active Learners
-
Design Your Dream InteriorsView Course
Sketchup
4.5 / 5
1500+ Reviews
Placement Assistance
Practical Training
Expert Faculty
MIT Certification
2 Weeks
Foundation
80+ Active Learners
-
Crafting Beauty in Every CornerView Course
3Ds Max
4.5 / 5
1500+ Reviews
Placement Assistance
Practical Training
Expert Faculty
Autodesk Certification
8 Weeks
Foundation
120+ Active Learners
-
Render Your Dreams with perfectionView Course
Vray
4.5 / 5
1500+ Reviews
Placement Assistance
Practical Training
Expert Faculty
MIT Certification
2 Weeks
Foundation
80+ Active Learners
-
Revolutionizing Industry with AutomationView Course
Electrical AutoCAD
4.5 / 5
1500+ Reviews
Placement Assistance
Practical Training
Expert Faculty
Govt. & Autodesk Certification
8 Weeks
Foundation
100+ Active Learners
-
Innovate, Automate, ElevateView Course
PLC Scada
4.5 / 5
1500+ Reviews
Placement Asistance
Practical Training
Expert Faculty
MIT Certification
8 Weeks
Foundation
120+ Active Learners
-
Precision Automation for a Smarter FutureView Course
E-Plan
4.5 / 5
1500+ Reviews
Placement Asistance
Practical Training
Expert Faculty
MIT Certification
2 Weeks
Foundation
100+ Active Learners
-
The Next Generation of AutomationView Course
HMI
4.5 / 5
1500+ Reviews
Placement Asistance
Practical Training
Expert Faculty
MIT Certification
2 Weeks
Foundation
100+ Active Learners
-
Empowering Industry through Intelligent AutomationView Course
MCC & VFD
4.5 / 5
1500+ Reviews
Placement Asistance
Practical Training
Expert Faculty
MIT Certification
2 Weeks
Foundation
90+ Active Learners
-
Design Your ImaginationView Course
Adobe Photoshop
4.5 / 5
1500+ Reviews
Placement Asistance
Practical Training
Expert Faculty
MIT Certification
8 Weeks
Foundation
100+ Active Learners
-
Where Creativity Meets TechnologyView Course
Indesign
4.5 / 5
1500+ Reviews
Placement Asistance
Practical Training
Expert Faculty
MIT Certification
8 Weeks
Foundation
90+ Active Learners
-
Artistry Meets InnovationView Course
Adobe Illustrator
4.5 / 5
1500+ Reviews
Placement Asistance
Practical Training
Expert Faculty
MIT Certification
8 Weeks
Foundation
90+ Active Learners
-
Transforming Ideas into ArtView Course
Coreldraw
4.5 / 5
1500+ Reviews
Placement Asistance
Practical Training
Expert Faculty
MIT Certification
8 Weeks
Foundation
100+ Active Learners

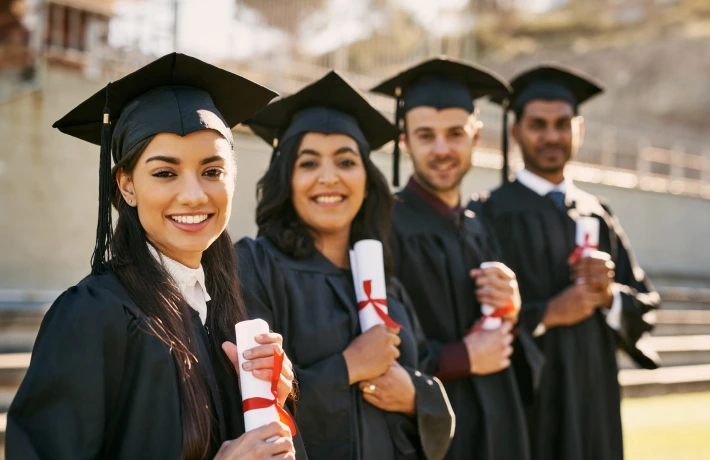
We build paths to success
At Milestone Institute, we bridge the gap between education and career success, providing placement support. Our dedicated team and industry connections ensure you land your dream job.
-
+
Enrolled Students
-
+
Company Tie-ups
-
+
Job Oriented Courses
Trace your own path with
Milestone
Milestone is here to guide you on your path to a successful career
Enroll for a free demo-
01
Call For Enquiry
Call us to schedule your visit and discover our campus firsthand.
-
02
Attend demo class
Attend a demo class and experience our teaching excellence.
-
03
Enrollment
Enroll in the course of your choice and begin your journey with us.
-
04
Projects
Work on industry-standard projects to build real-world expertise.
-
05
Interviews
Attend job interviews with top companies to launch your career.
-
06
Jobs
Secure your dream job in your field of expertise.
Why Choose
?
At Milestone, we make learning effortless and effective. As your trusted education partner, we provide top-notch technical training and personalized support, ensuring every student is job-ready. Our commitment to excellence ensures that every student receives the highest quality education and support. As one of the top CAD, BIM & IT software training institutes, we're dedicated to provide our students with an exceptional learning experience.
Register NowTop companies and brands look forward to
working with our students
-
Enrolling at MIT was a game-changer for me. I secured a job placement in just 8 months!
Ameya Rasam
-
I Joined MIT for Master's on my friend's suggestion, and it was the best decision i ever made.
Pratik Dubal
-
Personal Training from experienced faculty helped me to gain proper knowledge and skills.
Nikita Akhade
-
I got exactly what I needed, a fantastic learning experience with live industrial projects.
Nikita Shelar
Our students are placed in Top companies
Milestone Institute is committed to turning your academic education into a thriving career. With our master diploma courses, you'll receive personalized placement support and benefit from strong industry connections. Our dedicated team ensures you land a position at top companies, setting you up for future-ready success.
Learn More-
Abhay
-
Akshay
-
Vikrant
-
Anchal
-
Chetan Jadhav
-
Durga
-
Deepak
-
Amogh
-
Hemant
-
Ishan
-
Farhan
-
Jatin
-
Achal
-
Jeeshan
-
Kundan
-
Omkar
-
Pankaj
-
Pritam
-
Siddharth
-
Abhijit
-
Shweta
-
Saurabh
-
Sameer
-
Akshay
Course Curators
Get to know our dedicated team members who are here to support
your learning journey.
-
Naynesh Belhekar
Head Mechanical Design - Pennsylvania Transformer Technology Inc.
to a whole new level?